Síntesis
Compuesto por hormigón vibrado y comprimido de alta resistencia. Es un producto que se utiliza básicamente para suelos, pero ocasionalmente se utiliza como decoración sobre un cerramiento. De todas maneras este último no es el propósito de su fabricación. Son elaborados en fábrica, mediante una correcta dosificación de los materiales, luego estos materiales son vertidos en moldes y posteriormente, después del fraguado y secado, se realiza el curado. Es una herramienta ideal para aquellos proyectos donde el porcentaje de supercie impermeable es una limitante. Es absorbente y natural, y altamente resistente al tránsito de vehículos. Conforma la supercie ideal para patios o espacios de tránsito liviano y sendas peatonales ya que, dado su diseño, recrea un espacio fresco, verde y armónico. Se comercializa con tamaños entre 50x50cm y 30x30cm.
Contexto histórico, social y económico
La loseta críbada o también llamado adoquín de hormigón con insterticios no tiene un lugar de origen, ni un inventor particular. Es una evolución de un producto prevío muy utilizado y que gracias a la tecnología se pudo mejorar significativamente en muchos aspectos. Son económicos, de fácil y rápida instalación, tienen gran resistencia, no precisan de mucho mantenimiento, hay en muchos y variados diseños y colores, y se adaptan a cualquier tipo de terreno. La historia de los pavimentos con adoquines se inicia prácticamente con nuestra civilización. Cuando se construyeron la Vías Romanas se emplearon bloques de piedra trabajados especialmente para obtener una superficie lisa. La duración de estas vías, muchas de las cuales todavía se pueden visitar, es el mejor testimonio de la calidad de ejecución de dichos trabajos y de la factibilidad del sistema constructivo de pavimentos segmentados. Posteriormente aparecieron las superficies para el rodamiento de vehículos constituidas por adoquines de granito, ejecutadas durante muchos años en diversos países de Europa y luego en América, incluyendo nuestro país. Luego por el siglo XIX, con el desarrollo del hormigón como materia prima, trajo consigo la aparición de elementos prefabricados. Como por ejemplo, en nuestro caso que son los adoquines de hormigón. Son piezas de variadas formas que dependen de su aplicación, de hormigón comúnmente con una geometría tal que permite el ensamblaje con otras piezas idénticas para obtener una superficie continua. En general sus dimensiones permiten que puedan ser manejados con una sola mano o por una sola persona. No existe una fecha exacta del momento donde se empiezan a manufacturar estos adoquines prefabricados, pero hay datos y tablas del uso de estos en Europa y los Estados Unidos a mediados del siglo XX. Esto fue gracias al auge de la industria del hormigón durante este siglo, gracias a nuevas tecnologías durante la extracción, producción y transportacion del cemento Portland, que es la materia prima principal del hormigón. De allí derivó el producto que estamos estudiando, que es el Adoquín intertrabado de hormigón con intersticios. Estas pérforaciones en la superficie del adoquín ofrecen la posibilidad de ser rellenados con piedras, cesped o algun tipo de hierba logrando que este pavimento intertrabado combine belleza y estética a un muy bajo costo. pueden ser aplicados en jardines, plazas, terrazas de piscina, entradas de garage, garage, parques, plazas y aceras simplemente por su agradable apariencia visual. El uso de materiales reciclados como ingredientes del hormigón o concreto ha ganando popularidad debido a la cada vez más severa legislación medioambiental, así como la progresiva concienciación de la sociedad. Los ingredientes reciclados más empleados son las cenizas volantes, un subproducto de las centrales termoeléctricas alimentadas por carbón. El impacto ambiental de la industria del cemento es significativo, pero mediante el empleo de estos nuevos materiales se posibilita la reducción de canteras y vertederos, ya que actúan como sustitutos del cemento, y reducen la cantidad necesaria para obtener un buen concreto. Puesto que uno de los efectos nocivos para el medio ambiente es que la producción de cemento genera grandes volúmenes de dióxido de carbono, la tecnología de sustitución del cemento desempeña un importante papel en los esfuerzos por aminorar las emisiones de dióxido de carbono.
Definición ciencia
Esta compuesto por hormigon de alta resistencia. Son los mismos compuestos que tiene un hormigón común (cemento portland, grava, arena y agua), pero con algunas diferencias. Por ejemplo la relación de agua cemento es baja, el periodo de curado es mas largo, compactación del hormigón por presión y confinamiento de la mezcla en dos direcciones. Ademas es recomendable emplear alguno o una combinación de los aditivos químicos: superfluidificantes y retardantes; y, de los aditivos minerales, ceniza volante (fly ash), microsílica (silica fume) o escoria de alto horno.
Procesamiento
El clinker para el cemento previamente mencionado se extrae de canteras de caliza mediante la explosión de los suelos. Se pasan por una molienda, se cocina y luego se vuelve a moler uniformemente. Luego se le agregan arcillas y yeso. Los agregados, finos y gruesos se extraen de los fondos de los ríos, de las laderas de las montañas y de zonas arenosas. Las mejores arenas son las de río, que normalmente son cuarzo puro, por lo que aseguran su resistencia y durabilidad. Luego del transporte de los materiales a la fabrica se hace la mezcla, se vierte en el los moldes, se deja fraguar, secar, se desmolda, se cura y por ultimo se distribuye.
Propiedades
Normas
NORMA | TÍTULO |
IRAM 11656 | Requisitos y Métodos de Ensayo – Adoquines de Hormigón para pavimento intertrabados. |
IRAM 11561-2 | Requisitos Bloques No Portantes de Hormigón 3.2 Bequisitos del Producto, 3.3 Tolerancia, 3.4 Terminación y Apariencia. |
IRAM 11561-1 | Bloque de Hormigón. Vocabulario |
IRAM 11657 | Adoquines de hormigón para pavimentos intertrabados. Requisitos para su colocación y recomendaciones sobre la estructura básica. |
Puesta en obra
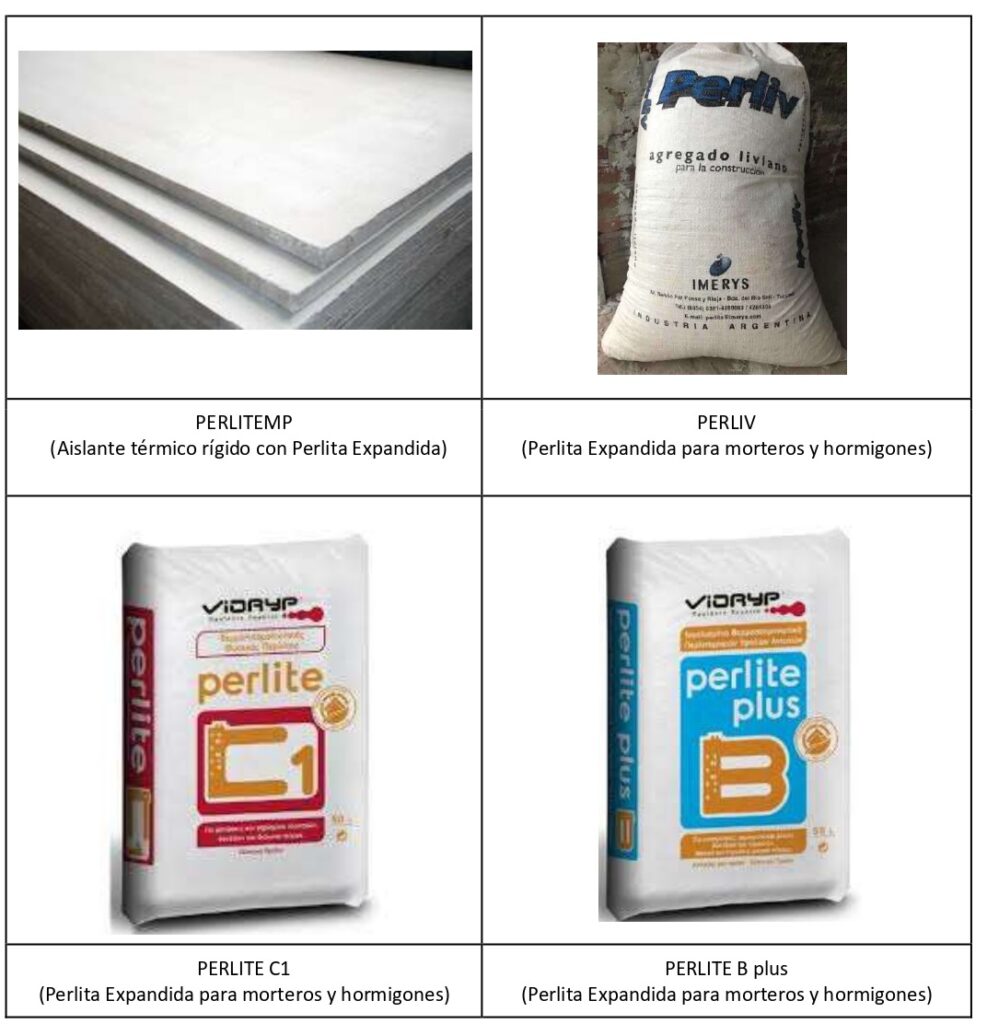
Proveedores
Distribuidor | Formato | Nombre | Origen | Marca |
http://www.pavitec.com.ar/losetacribada.html | Loseta con 6 modulos Medidas: 45x30x8 cm | Loseta Cribada Pavitec | Argentina | Pavitec |
http://www.bloky.com.ar/cesped.html | Loseta con 6 modulos Medidas: 50x33x10 cm | Bloky Hierba | Argentina | Bloky |
http://moriblock.com.ar/adoquin-verde-block/ | Loseta con 4 modulos Medidas: 40x40x8 cm | MoriBlock Verde Block | Argentina | MoriBlock |
http://www.adoquinesdehormigon.com.ar/12-loseta-cribada-greenblock-.html | Loseta con 4 modulos Medidas: 40x40x10 cm | Loseta Cribada Green Block | Argentina | SuperBlok |