Síntesis
El mosaico veneciano, también conocido como venecita, es un producto vítreo creado hace más de 2500 años. Para su realización se funden materias primas naturales como la sílice, base del vidrio, y otros componentes minerales. El color se incorpora en la misma masa de composición. Es un producto único que perdura en el tiempo y no sufre ningún tipo de cambio, tanto en su color, como en la dilatación o contracción, ya que en el proceso de fusión la temperatura que alcanza el mosaico veneciano es de 1400 grados centígrados. Usualmente el material se consigue en placas de 30cm x 30cm, ya que están compuestas de 225 piezas de 2cm x 2cm cada una. La variedad de colores es infinita. Originalmente este material no se creó para utilizar como un revestimiento, sino para la producción artística. Actualmente se usa tanto en lo artístico como en construcciones, ya sea en baños, cocinas, piscinas, etc.
Contexto histórico, social y económico
El cerámico veneciano comenzó utilizándose aproximadamente en el 2500 a.C en Asia, en la rama del arte por artesanos, ya que la gran variedad de colores les permitía elaborar innumerables piezas decorativas. El descubrimiento de sus potenciales propiedades convirtió un elemento que nació para el arte, en un producto creativo pensado para vestir los ambientes. Al ser un material resistente al agua, se comenzó a utilizar como revestimiento en baños, cocinas y piscinas, donde las paredes están expuestas a la humedad y a la suciedad y deben ser fáciles de limpiar, y dónde están en constante contacto con el agua sin salir perjudicadas.
El vidrio se utilizó en mosaicos ya en el año 2500 a. C., situándose en la Mesopotamia asiática con el propósito de crear imágenes que perduren en el tiempo. Hasta el siglo III a. C., antes de que artesanos innovadores en Grecia, Persia e India crearan azulejos de vidrio, se utilizaba el vidrio partido en fragmentos, donde todas las piezas eran desiguales. Antiguamente se utilizaba para rendirle culto a los dioses a través de grandes retratos en mosaicos que decoraban las paredes de los templos. Mientras que las baldosas de arcilla datan de 8000 aC, había barreras significativas para el desarrollo de las baldosas de vidrio, incluidas las altas temperaturas requeridas para fundir el vidrio y las complejidades de dominar varias curvas de recocido para este.
Como anteriormente se dijo, en los inicios de material, era exclusivamente utilizado en artesanías, luego, se extendió su uso hasta llegar a la construcción. Se utiliza como revestimiento que sirve tanto como aislación térmica como hidrófuga. Su implementación en la construcción facilitó muchos problemas ya que es un material resistente a las manchas, a los productos químicos, a los aditivos para piscinas, y a los ácidos. Por otro lado, tienen nula absorción de agua, son resistentes a los cambios térmicos, a la abrasión, al hielo, y no poseen modificaciones con la luz. En definitiva, es un material altamente duradero.
Actualmente, la mayoría de las industrias de cerámico veneciana optan por elaborar el material a través de vidrio reutilizado, es decir, reciclan botellas u otros elementos de vidrio y los funden para obtener el vidrio en estado viscoso y maleable, apto para ser moldeado. A su vez, las industrias eco-friendly implementaron el uso de maquinaria eléctrica, con el fin de reducir la contaminación ambiental emitida por los gases.
A la hora de escoger un revestimiento, el cerámico veneciano se posiciona entre los más aptos y económicos del mercado, y de fácil colocación. Para la correcta colocación de las venecitas los especialistas recomiendan utilizar adhesivos de primera marca para revestimientos de baja absorción. Simplemente se coloca la mezcla de manera uniforme sobre la superficie, se coloca la placa de cerámico, y cuidadosamente se extrae el papel
contenedor. Se lo deja secar por unos minutos, para asegurarnos que esté firme, y se procede a colocar el tomado de juntas. Una vez seco se extrae el excedente, y se limpia con un paño húmedo para asegurarnos que no quede mezcla en la superficie opacando el mosaico.
El cerámico veneciano está compuesto principalmente de sílice, éste es un elemento químico metaloide que se encuentra en abundantes cantidades en la corteza terrestre. Su explotación es a través de canteras de arena, luego, la arena pasa por un proceso a través de hornos que llegan a una temperatura de 1900°C donde se le extrae el sílice al elemento. Uno de los principales problemas que surgen de su extracción radica en la salud de la población que se encuentre cerca de la cantera, puesto que dicha acción levantará nubes de polvo de sílice muy fina y muy peligrosa ya que su inhalación posibilita desarrollar una forma de cáncer en los pulmones llamada ’’silicosis’’, sin contar el daño que genera en la corteza. Dicho cerámico es reutilizable, ya que se lo puede fundir a elevadas temperaturas, y volver a moldear.
Definición ciencia
El material se compone de sílice, pigmentos y otros aditivos. El sílice se extrae de la arena y es un elemento que tras su composición también se lo conoce como vidrio. La base del color en general son los pigmentos, en cerámica los pigmentos que se utilizan son de origen mineral, obtenidos de tierras, fósiles, rocas, en forma de silicatos, carbonatos o sales. Estos pigmentos deben pasar por un proceso de combustión a altas temperaturas y luego por un proceso de molienda hasta obtener el tamaño de partícula deseada. Son térmicamente estables, mantienen sus propiedades al paso del tiempo y son resistentes a ácidos y abrasivos.
Procesamiento
El procesamiento para la fabricación del cerámico veneciano parte principalmente de la extracción de la arena de las canteras. Este material se transporta a la fábrica donde pasa por una serie de procesos para extraerle el sílice, el cual es el componente principal de dicho cerámico. Para lograr esto, la arena debe pasar por hornos que reducen el óxido a temperaturas superiores a 1900°C. El sílice se acumulará de forma líquida y se extraerá para luego enfriarlo. Seguido a esto, el material se mezclará junto a otros componentes minerales y los óxidos que le darán color para luego ser fundido a 1600°C. Una vez fundido, el material pasa por una prensa, donde una máquina irá moldeando y marcando los cuadrados característicos del mosaico. Por último, se deja enfriar el material para poder pasar a la siguiente fase, donde se separarán y se pulirán los cuadrados ya marcados en la etapa anterior.
Propiedades
TIPO DE PROPIEDAD | PROPIEDAD O CARACTERÍSTICA | VALOR TÍPICO |
Físico – química | Densidad | 2,66 kg/m3 – (10-B) |
Resistencia ambiental ¹* | A I B I C I D I E I F I G | |
Mecánica | Resistencia a la compresión | 2500 MPa – (10-C) |
Resistencia a la tracción | 370 MPa – (10-C) | |
Dureza Knoop | 2500 HK – (10-C) | |
Térmica | Resistencia a altas temperaturas – Punto de fusión del material | 2700oC (10-A) |
Coeficiente de expansión térmica | 4,7-7,6 x10-6 K-1 – (10-D) | |
Conductividad Térmica a 0-100C | 80-150 W m-1 K-1-(10-D) |
NORMA | TÍTULO |
‘’UNE-EN’’ ISO 105452 | Baldosas cerámicas. Parte 2: Determinación de las dimensiones y del aspecto superficial. (ISO 10545-2:2018) |
ISO 10545-7 | Determinación de la resistencia a la abrasión |
ISO 10545-12 | Determinación de la resistencia a la helada |
ISO 10545-13 | Determinación de la resistencia química |
ISO 10545 14 | Determinación de la resistencia a las manchas |
ISO 10545-17 | Determinación del coeficiente de fricción |
Puesta en obra
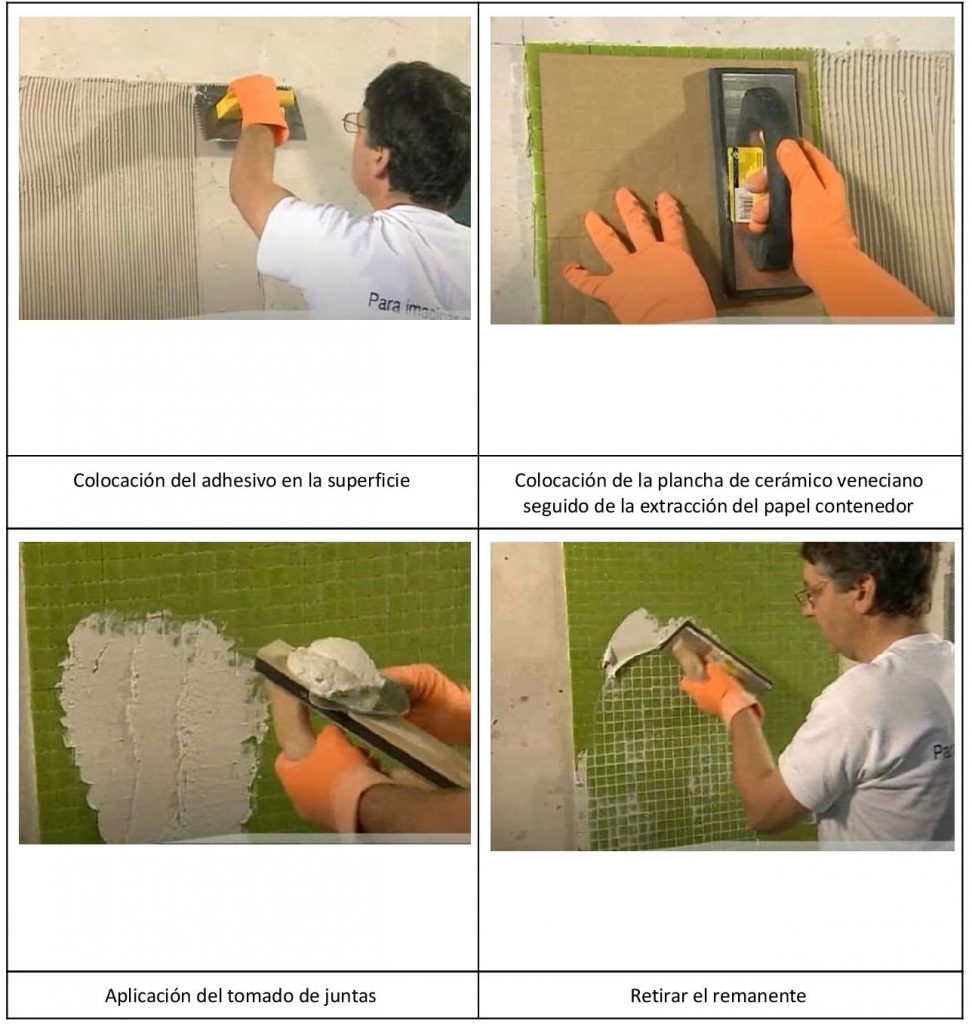
Proveedores
DISTRIBUIDOR LOCAL | FORMATO | NOMBRE | ORIGEN | MARCA |
https://www.ceramicasanl orenzo.com.ar/ Fabricante y distribuidor de cerámicos | Placas de 33x33cm | Cerámico veneciano | Argentina | San Lorenzo |
http://www.ceramicacanu elas.com.ar/ Fabricante y distribuidor de cerámicos | Placas de 32x47cm | Venecitas | Argentina | Cerámica Cañuelas |
http://murvi.com.ar/ Fabricante y distribuidor de cerámicos | Potes de 800gr | Mosaico veneciano | Argentina | Murvi |
http://www.vetrovenezian o.com.ar/index.html Fabricante y distribuidor de cerámicos | Placas de 33x33cm | Venecitas | Argentina | Vetro Veneziano |
https://mosaicosvenecian osdemexico.com/ Fabricante y distribuidor de cerámicos | Placas de 30x30cm | Mosaico veneciano | México | Mosaicos venecianos de México |
https://dune.es/ Fabricante y distribuidor de cerámicos | Placas de 30.5×30.5 cm | Mosaico | España | Dune |
https://www.sodimac.com .ar/ Distribuidor | Placas de 30x30cm | Mosaico | Argentina | Piú |
Bibliografía
- Uso del cerámico veneciano en la construcción : A –https://decoracion2.com/opendeco/venecitas-para-decorar-tus-paredes-de-manera-diferente/ B – https://promateriales.com/pdf/PM-95-6.pd f
- Características y propiedades del material: https://mosaicoveneciano.wordpress.com/about/
- Historia del origen del material: https://arqa.com/empresas/novedades/mosaico-veneciano-su-historia.html
- Proceso de fabricación : https://www.insst.es/documents/94886/161971/Cap%C3%ADtulo+84.+Vidrio,+cer%C3%A1mica+y+ma teriales+afines
- Normas ISO: http://www.qualicer.org/recopilatorio/ponencias/pdfs/9411060s.pd f
- Noticia de daños ambientales causados por extracción del silicio: http://www.laizquierdadiario.com/Las-peligrosas-canteras-de-arena-siliceas-en-el-valle-inferior-del-Rio-C hubut
- Correcta colocación del revestimiento : http://www1.rionegro.com.ar/diario/tools/imprimir.php?id=8908
- Información sobre el Silicio: https://siliciorganico.es/de-donde-y-como-se-obtiene-el-silicio/
- Información sobre la pigmentación del material: https://es.slideshare.net/iriasalas30/el-color-en-la-ceramica
- Ficha técnica: A : http://www1.frm.utn.edu.ar/cmateriales/Trab.%20Inves.(alum)/materiales%20ceramicos.ht B: https://es.slideshare.net/stmjhh/materiales-ceramicos-63273215 C: https://www.monografias.com/trabajos81/introduccion-materiales-ceramicos/introduccion-materialesceramicos2.shtml D:http://www.goodfellow.com/S/Silicio.html