Síntesis
Tablero que se obtiene mediante encolado de chapas de madera superpuestas de modo que sus fibras formen un ángulo determinado, generalmente recto.Se pueden utilizar como revestimientos chapas de madera decorativa, plásticos, papel impregnado en resinas sintéticas, pintura, tintes, chapas metálicas, etc. Los tableros utilizados en aplicaciones decorativas se rechapan en la cara vista con maderas finas y en la no vista con una madera de menor calidad para equilibrar el tablero.La presentación más común de este material es en tableros de 4×8 piesHYPERLINK “https://es.wikipedia.org/wiki/Pie_(unidad)”, 1,22×2,44 metros, en grosores que van de los 3 mm hasta los 36 mm en casi cualquier tipo de madera, predominando las maderas blandas. Existe una gran variedad de madera contrachapada.
Contexto histórico, social y económico
Los contrachapados se han hecho durante miles de años,su elaboración se ha dado en distintos lugares y circunstancias a lo largo de la historia, sin que estén relacionados entre sí.Según algunos autores, los egipcios habrían sido los inventores del tablero contrachapado. En sentido estricto no es así ya que el contrachapado requiere chapas finas, adhesivos fuertes y presiones importantes, medios que no se encontraban al alcance de esta civilización. Es cierto que se trabajaba el chapado con gran maestría en mueble y otros objetos (son famosas las sandalias de Tutankamon a base de madera y otros materiales). En algún relieve egipcio se aprecia la labor de chapado: con unas grandes cuchillas se corta la madera, mientras en un puchero se cuece la cola animal, después se aplica la chapa encolada sobre la superficie y se aplica presión mediante sacos.
El tablero contrachapado es el primer intento, y acierto, para conseguir madera reconstituida técnicamente, o de ingeniería con un doble fin: obtener un producto más homogéneo y de mayor calidad junto con un mejor aprovechamiento de un recurso forestal cada vez más escaso.Una de las actividades que más hizo adelantar la aparición del contrachapado fue la construcción de claves y pianos a partir del siglo XVII. Las curvadas cajas de armonía y de resonancia de estos grandes instrumentos se solucionaba mediante laminado al hilo de diferentes capas de chapas. También en carpintería y ebanistería se ejecutaban piezas curvas a base de laminados.Existe gran cantidad de posibilidades en cuento a la aplicación de este material hoy en dia,se lo puede ver por ejemplo en una construcción de viviendas con vetas a la vista,mueblería, decoración de interiores, elementos expuestos a la intemperie,recubrimientos estructurales de pisos, muros y techos ,prefabricación de elementos de construcción,se puede utilizar también en moldajes para hormigón y elementos estructurales en la construcción, agroindustria, contenedores y transporte
Los problemas ambientales asociados con la fabricación de tableros y productos de madera particuladaincluyen:Prácticas forestales sostenibles ,emisiones a la atmósfera ,aguas residuales ,materiales peligrosos ,residuos sólidos y Ruido. Cuando se utilizan troncos en vez de residuos de madera como fuente de fibra el principal impacto ambiental de la fabricación atañe al manejo de los recursos forestales. Las cuestiones relativas a las prácticas forestales sostenibles se describen en las Guías sobre medio ambiente, salud y seguridad para el Manejo Forestal. Este tipo de impactos puede reducirse mediante un mayor uso de fibras recicladas o recuperadas en la fabricación de tableros. Los procesos de producción de tableros y productos de madera particulada pueden generar una amplia gama de emisiones a la atmósfera, dependiendo del método empleado. Los contaminantes derivados de los procesos de combustión incluyen materia en partículas (MP), óxidos de nitrógeno (NOx), monóxido de carbono (CO) y óxidos de azufre (SOx) generados por calderas radiantes, generadores de aire caliente y calentadores de fluidos térmicos. Los aldehídos (incluido el formaldehído) y otros compuestos orgánicos volátiles (COV) se liberan al calentarse la madera en secadores de partículas, secadores y prensas de chapado de madera y al enfriarse los tableros prensados.
Definición ciencia
Los materiales que entran en su composición son: chapas o capas de madera, adhesivos y revestimientos.Las chapas son láminas de madera que no sobrepasan los 7 mm de espesor.La gran mayoría de las especies de madera son desenrollables y aptas para obtener chapa pero las más habituales son las ‘maderas finas’ de haya, nogal, roble, chopo, pinos sivestre, insignis y oregón, chopo, abedul o tropicales como okume, embero, mansonia, mongoy, mukaly, samba, sapelly, ukola, etc.Las chapas para tableros se clasifican por la presencia de peculiaridades de la madera (principalmente nudos) en tableros estructurales o bien por su estética y figura en tableros decorativos para cara o contracara.AdhesivosDependiendo del uso y de las características del tablero se pueden usar adhesivos de urea formol para interiores y de urea formol reforzadas con melamina o fenol formaldehído, para exteriores.
Procesamiento
Los troncos se montan en una máquina que los hace girar para realizar el corte, a fin de generar una hoja de chapa, que se corta a las medidas apropiadas. Luego, esta chapa se procesa en una estufa para madera, se parchea o arregla en sus eventuales imperfecciones y, finalmente, se pega a presión(los tableros contrachapados se construyen con un número impar de capas con el grano de capas adyacentes perpendiculares,las capas constan de una sola lamina o dos de ellas paralelas a la dirección del grano) y a una temperatura de 140 °C, formando así el tablero de contrachapado. Estos tableros se pueden cortar, parchear, pulir, etc., según el uso que se le vaya a dar.
Propiedades
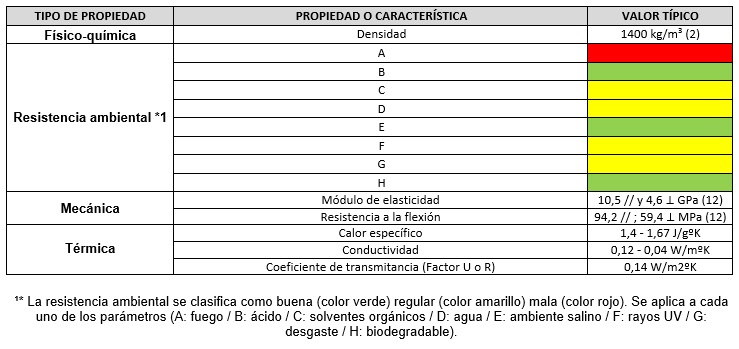
Normas
NORMA | TÍTULO |
EN 13.896 | Comportamiento al fuego |
ISO 14001 | Certificación Sistemas de Gestión Ambiental |
ISO 14006 | Certificación Gestión ambiental del proceso de diseño y desarrollo, Ecodiseño |
EN 717-2 | Determinación de la emisión de formaldehído |
ISO 166002 | Certificación Gestión de la I+D+i |
EN-314-1 | Calidad del encolado |
Puesta en obra
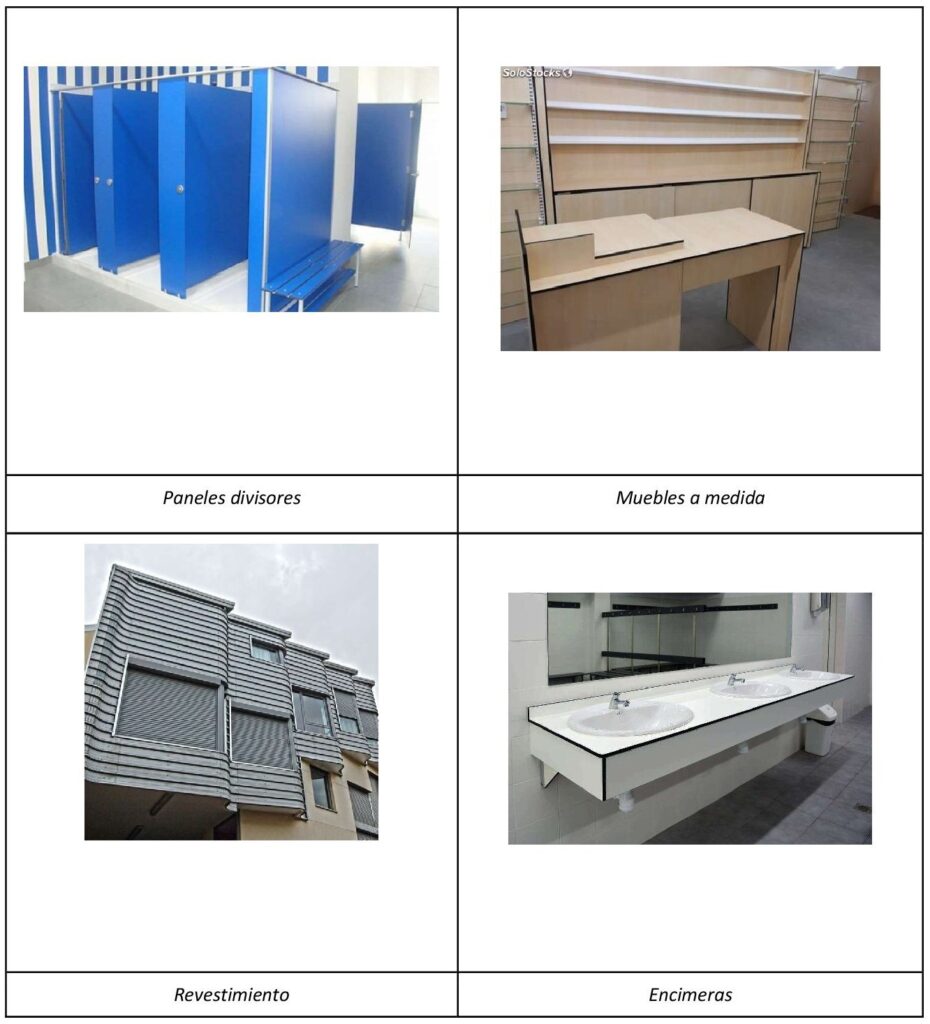
Proveedores
MARCA | ORIGEN | NOMBRE | FORMATO | DISTRIBUIDOR LOCAL |
Coama | Argentina | Machimplak | *Placascon medidas completamente adaptables a la necesidad del cliente. *1.22×2.44. | Coama (54-11) 4871 – 5977 / 5905 www.coama.com.ar Av. de los Lagos 6855 |
DAC | Argentina | Mult.Fenolico | * Placasfenólicas de 18mm de espesor * 275x183cm* 260x183cm | DAC Maderas (11) 6636-7855 www.dacmaderas.com.ar Av. 101 Dr. Ricardo Balbín 3342 |
Egger | Argentina | Placa CompFenolico | *Placas fenólicas de 18/11 mm de espesor *1.22×2.44 | Easy 0810-999-EASY www.easy.com.ar Av. Brig. Gral. Juan Manuel de Rosas 658 |
Madersama | Argentina | Placa Compensado Fenólico | * Placasfenolicas6, 9, 12, 15 y 18 mm de espesor * 2440 x 1220 mm | Madersama (3751)-531450 taedasa.com.ar Camarones 3952,CABA |
Bibliografía
1 | www.fenoltec.com (Ficha tecnica) |
2 | https://infomadera.net/uploads/productos/informacion_general_142_contrachapado.pdf (Tableros contrachapados) |
3 | https://infomadera.net/uploads/productos/informacion_general_404_Tableros%20Estructurales_18.07.2011.pdf (“TABLEROS ESTRUCTURALES DERIVADOS DE LA MADERA”) |
4 | www.portalhuarpe (Instalaciones I climatización en la arquitectura) |
5 | http://www.maderasmisiones.com.ar/productos.asp?cat=160(ficha,cualidades propias del fenólico) |
6 | www.fenoltec.com (Ficha tecnica) |
7 | https://core.ac.uk/download/pdf/61519912.pdf(Comparación de ensayos a compresión de madera estructural) |
8 | http://aserraderonelson.com.ar/product/fenolicos/(cualidades del panel fenólico) |
9 | http://publiditec.com/blog/tableros-contrachapados-madera-para-la-construccion/ (Tableros contrachapados de madera para la construcción) |
10 | https://www.woodproducts.fi/es/content/madera-contrachapada (CATEGORÍAS DE CALIDAD DE LA MADERA CONTRACHAPADA) |
11 | http://www.cscae.com/area_tecnica/aitim/actividades/act_paginas/libro/11%20Tableros%20contrachapados.pdf ( |
12 | https://www.maderastpf.com/pdfs/Tablero_contrachapado_fenolico_plastificado.pdf, visitado 16/04/2021 |